POF Termination and Insulation
How are fiber optic cables insulated?
Plastic optical fiber, being made of an insulating material, does not conduct electricity. This allows it to be used in flammable or explosive environments, and causes it to be immune to electromagnetic interference (EMI) and keeps connected devices electrically isolated. This makes it highly suited for use in industrial applications such as machine control.
POF cables still incorporate an outer jacket that protects the fiber inside from the environment. Depending on the application the fiber is used in, different materials and thicknesses of jacket may be desired.
How are fiber optic cables terminated?
Terminating fiber optic cables starts with a process called finishing. This is where the of the end of fiber and the ferrule that holds it in the connector are polished to give a uniformly flat and clear surface for the best optical performance and minimal signal loss. Historically, finishing has taken the form of the tedious task of sanding the fiber’s end with fine sandpaper. Once this is complete, a connector is placed on the fiber and is crimped or glued into place.
Simple termination methods are one of the major advantages to plastic optical fiber. Terminating POF can be done without polishing at all, making for easy field installations, with no glass fibers shards to handle or dispose of.
Connectorless systems also exist, such as Firecomms’ OptoLock® series, where the terminated fiber is placed into a receptacle containing the active optical components and is clamped into place.
Finishing and terminating at FiberFin
FiberFin uses a proprietary process for finishing the POF used in all of its products. This is done using hand techniques described below, as well as automatic machines built and designed in-house. We also offer tools such as the FF-STD-2 hand tool for finishing fibers in field installations.
FiberFin offers a wide selection of connectors for sale and in manufactured cable assemblies, including LC, SMA, SMI, and other, legacy connectors, as well as components for the OptoLock® connectorless system.
Polishing and Lapping
One of the biggest differences between silica (glass) fiber and plastic optical fiber are polishing techniques. Polishing plastic often causes it to deform and gives it a matte finish without the proper technique. The following is s step-by-step guide for finishing plastic optical fiber cable by hand and terminating with Broadcom connectors.
Tools required
- Wire cutters
- 16 AWG latching wire strippers, such as Stripmaster™ Type 45092
- Crimping tool, such as FF-HTCRMP-1
- Polishing kit, such as FF-LCP-HPPOL-K
- 10x magnifying glass (minimum, for inspection)
- Workbench light source (for inspection)
Materials required
- Plastic optical fiber cable, such as Agilent HFBR or Mitsubishi ESKA®
- Connectors; These instructions cover any of the following:
- HFBR-4501/4503 Gray Simplex Latching Connector and HFBR-4525 Crimp Ring
- HFBR-4511/4513 Blue Simplex Latching Connector and HFBR-4525 Crimp Ring
- HFBR-4506 Parchment Duplex Connector and HFBR-4526 Duplex Crimp Ring
- HFBR-4516 Gray Latching Duplex Connector and HFBR-4526 Duplex Crimp Ring
Step 1
If terminating a duplex POF cable, separate the channels approximately 50mm (2.0 inches) from the cable’s end.
After cutting the cable to the desired length, strip off approximately 7mm (0.3 inches) of the outer jacket with the 16 AWG wire strippers. When using a duplex connector on duplex cable, the separated channels must be stripped to equal lengths to allow for easy and proper insertion of the cable into the connector.
Step 2
Place the crimp ring and connector over the end of the cable. The fiber should protrude about 3mm (0.12 inches) through the end of the connector. Carefully position the ring so it is entirely on the connector, with its rim flush on the connector, leaving a small space between it and the flange. Crimp the ring in place with the crimping tool.
By convention, gray connectors denote transmitting ends of cables, and blue connectors denote receiving ends.
A two-part epoxy (part # FF-GMEPXY 1656) can be used for applications that require better retention between the cable and connector. Place the adhesive into the connector before inserting the fiber and crimp as described above. The connector can be polished (step 3) after the epoxy has cured, typically 24 hours after application.
Step 3
Cut the excess fiber from the connector, leaving 1.5mm (0.06 inches) extending from the end.
Insert the connector into the polishing fixture with the tripped fiber protruding from the bottom of the fixture. The fixture specified above can be used to polish two simplex connectors simultaneously, or one suplex connector.
Place the 600 grit abrasive paper on a flat, smooth surface. Pressing down on the connector, polish the fiber and connector by making figure-eight pattern strokes on the paper until the fiber is flush with the bottom of the polishing fixture. Wipe the connector clean with a cloth or tissue.
The four dots on the bottom of the polishing fixture are wear indicators. Replace the fixture when any of the dots are no longer visible. Typically, they can be used 10 times to polish 10 duplex connectors or 20 simple connectors.
Step 4
Place the flush connector and polishing fixture on the dull side of the 3μm pink lapping film and continue to polish the fiber and connector using approximately 25 figure-8 strokes. The fiber end should be flat, smooth and clean afterward. After cleaning the connector end, the cable is ready for use.
This step results in an 2 dB improvement in coupling performance between the cable and transcevier over the 600 grit polish alone. This may be omitted where this improvement is not essential.
Hot Plate Finishing
A pad or mirror plate is headed up to 150°C to 200°C. When a connector comes in contact with the heating pad, it melts the POF resin and fills the voids of the chamfer in the connector housing. For the amount of time required and the cost of the equipment involved, this technique gives good finishes. However, the skills required for consistent results and costs special equipment and connectors may make this technique impractical for some applications.
Tools required
- Wire cutters
- Wire strippers
- 10x magnifying glass (minimum, for inspection)
- Workbench light source (for inspection)
Materials required
- Plastic optical fiber cable
- Hot melt connectors
Step 1
Turn on the hot plate and allow it to warm up for about 2 minutes.
Step 2
Cut the POF cable to the desired length, leaving approximately 10mm (0.4 inches) for cutting or finishing errors.
Step 3
Stip the POF cable ends to the length specified by the connector’s manufactuer, and insert the fiber into the connector. Connector housing assembly may require crimping or gluing; refer to the documentation provided by the connector’s manufacturer.
Step 4
Place the connector into the hot plate’s connector holder, and press it lightily against the mirror finish on the hot plate. The hot plate will typically have an indicator that turns on indicating that finsihing is underway, and another to indicate that it is complete. This takes 6 to 8 seconds.
Continue to hold the connector against the hot plate for at least another 5 seconds after the process completes to give the connector time to cool and cure.
Remove the connector and inspect the polished surface for defects. If the surface appears to have an acceptable finish, the cable is ready for testing and use.
Razor Blade Finishing
FiberFin offers several different tools for razor blade finishing that give the best finishes of any razor blade tool on the market.
Razor Hand Tools
The All-In-One Professional hand tool (FF-STD-2) was tailored for the installer, allowing them to finish and strip POF cable with consistent results. Average attenuation losses are between 1.0 and 1.5 dB.
View finishing hand tools in the store
Razor Cutters
FiberFin’s ultra low-loss razor cutters are also all-in-one tools for POF terination. While there are numerous other razor cutters on the market, FiberFin’s give the best finishes with attenuation losses of 0.8 to 1.2 dB, thanks to the patented blade and blade placement technique used.
Each tool is designed for a specific connector, and can be used to slit duplex zip cord and strip off the fiber’s jacket.
With ultra low loss finishes, cable assemblies can be up to 15 meters in length longer, or subject to additional bends in installations. (Based on an average transmission loss of 160 dB/m for step-index POF).
[arve url=”https://www.youtube.com/watch?v=k48ZrXIr1Pk” maxwidth=”500″ align=”center”]
View razor cutters in the store
Machine Finishing
The FiberFin® finishing process is the culmination of years of research and development in a POF termination technique that gives consistently high-quality finishes. The process involves a single crystal diamond that polishes a fiber’s surface to a mirror finish a matter of seconds.
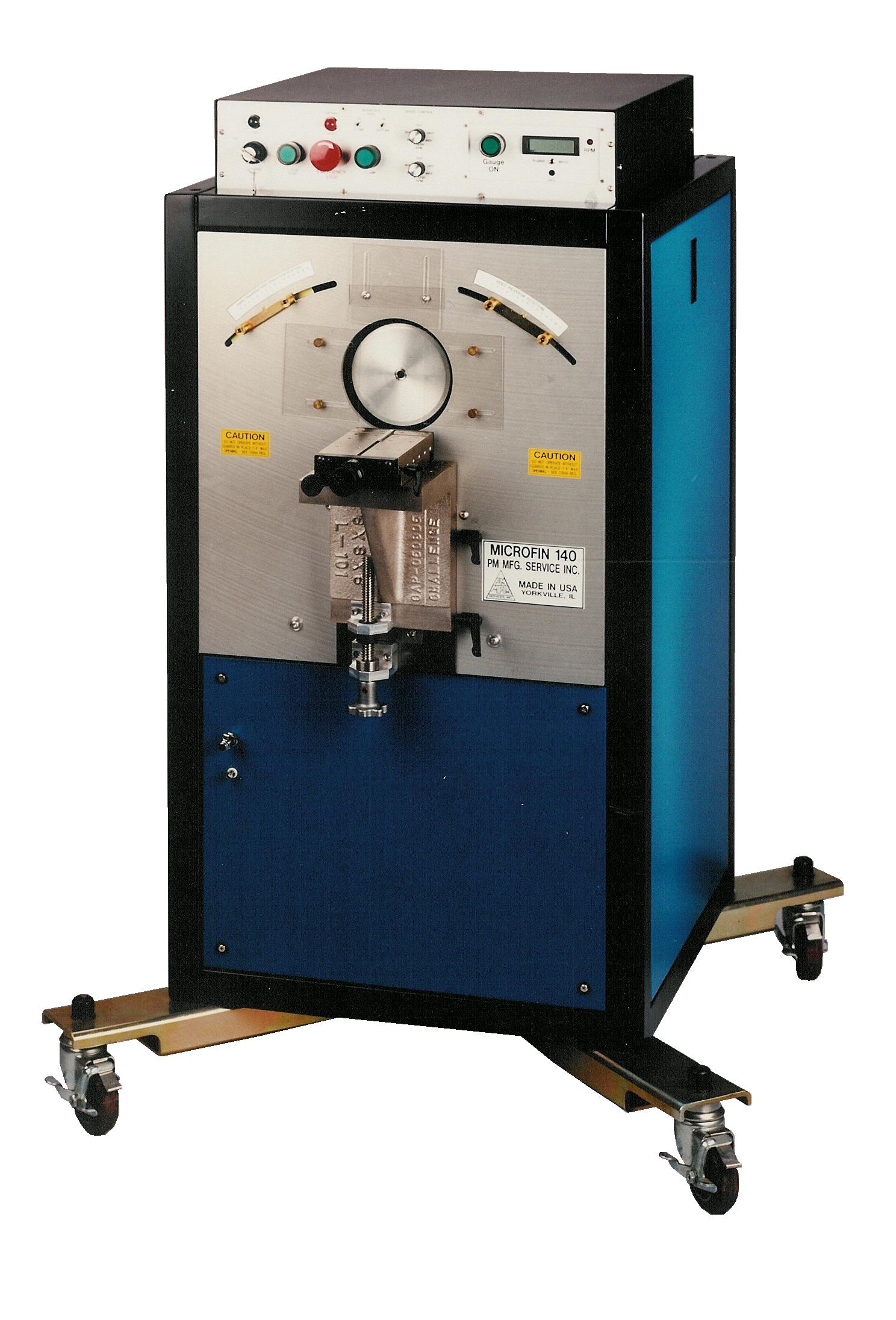
The goals of the FiberFin® process are speed, consistent results, minimal learning curves, and the lowest cost per termination. Since the development of the process, FiberFin has built several machines that meet these goals and are used every day in its production facility, and are available for lease.
The FiberFin 140 was the first FiberFin machine, built to finish fibers up to 140mm in diameter. It has been used worldwide in applications ranging from univerities and laboratories to high-energy physics experiments.
The FiberFin 4 is our top-of-the-line benchtop finishing machine, capable of finishing fiber up to 6mm in diameter. In addition to these, the FiberFin 5 and FiberFin 10 have been built for exclusive in-house use.
Read more about our facility and equipment
References
A. Weinert., Plastic Optical Fibers. Munich, Germany: Publicis MCD Verbeagentur GmbH, 1999.