How do fiber optic sensors work?
While fiber optic cables can be used to connect remote sensors to electronic loggers or signal processors the same way that copper wires can, they can also be used as sensors themselves. This is possible because when a fiber undergoes a physical change, such as bending, the light passing through it undergoes changes that are detectable under the right circumstances.
So far, this method has been used to detect temperature changes, acceleration, rotation, pressure, mechanical strain, as well as presence of chemicals, all through careful engineering of the fiber’s core and cladding materials and light-sensing technology. The Wikipedia article on fiber optic sensors provides an overview of the various applications.
This is the fastest developing field within fiber optics. As an engineering company, FiberFin is proud to be working with other companies on the leading edge of these developments.
POF Sensor Products
FiberFin offers products specifically designed for the wide variety of sensor applications that POF is used in.
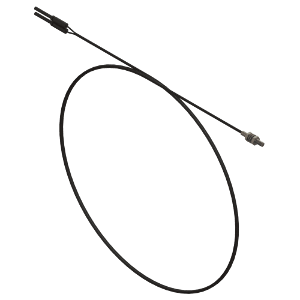
Sensor Cable Assemblies
Cable assemblies built with sensor ferrules, specifically designed for POF sensor applications
POF Sensor Basics
There are three common methods for measuring external forces using plastic optical fiber. From these, other techniques are derived and used with highly specialized types of POF to create precise and accurate sensors.
Intensity Modulation
Intensity modulation is the simplest method, requiring only three components: A light source, a photo detector, and a measurement instrument such as a multimeter or DAQ. As the fiber undergoes physical changes, such as being compressed or flexed, the light signal transmitted through it is attenuated, reducing the intensity at the end of the fiber. By measuring the final intensity and comparing it to a known state, it is possible to draw conclusions about the physical state of the fiber. Sometimes cuts or abrasions are made to the sensor fiber that cause it to respond strongly to specific forces.
Phase Modulation
Phase modulation is used in sensor applications where involving two loops of POF. Light is transmitted through both loops, with one loop designated for sensor measurement, and the other for reference. By bending or stretching the sensor fiber, the phase of the light signal changes, and a difference between it and the reference signal become apparent. The reference loop is usually placed near the sensor loop to compensate for the effects of temperature and other external forces that affect the whole system.
Bragg Wavelength Shift
Bragg Wavelength Shift involves monitoring the color of the light that is transmitted through a section of fiber called a Bragg Grating. This has periodic variations in its cross-section that cause the wavelength, and consequently the color, of the light to vary as the fiber itself expands and contracts. By measuring the wavelength of light and comparing it to a reference, the amount of strain on the fiber sensor can be determined.
Advantages of POF Sensors
POF is not only an inexpensive material to make sensors out of, is intrinsically safe due to its chemical resistance and inert properties. Extensive testing carried out by López et al. has also shown that it is unaffected by extreme changes temperature during operation.
Example Sensor Applications
Liquid Level Detection
Noverflo has developed a POF sensor that uses a patented fiber geometry to modulate the intensity of a light signal, based on how much of the fiber is submerged in a fluid with a different refractive index. It can be used to detect liquid levels in fuel tanks, oil sheens above water, and the presence of ice.
Bacteria Detection
Researchers at the Photonics and Instrumentation Laboratory at Federal University of Rio de Janeiro created a POF-based biosensor capable of detecting the presence of the bacterial pathogen Escherichia coli in water. This was done by replacing its cladding with hexamethylene diamine (HDMA) and E. coli antibodies through a process of functionlization. The rest of the instrumentation was based on a microcontroller, LED light source, photodiode, and operational amplifier. The resulting system was capable of detecting E. coli concentrations as low as 10-3 UFC/m.
Rotary and Linear Position Sensing
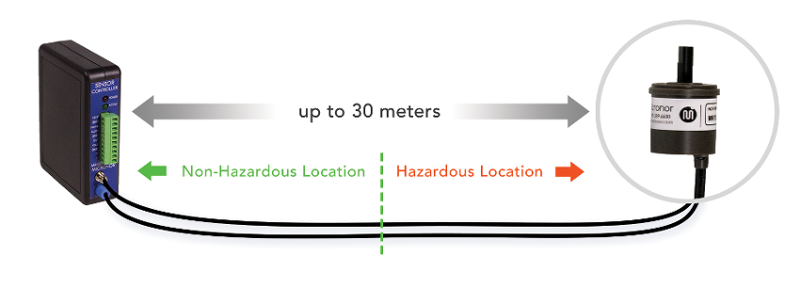
Micronor, in collaboration with Air Force Research Laboratories, has developed absolute position sensors that are designed specifically for the harsh environments of airframes. These feature non-metallic construction, and resolution of less than 0.1° or 10μm. They make use both multi-core imaging fiber and solid-core fiber from Asahi Kasei. They work on the same principles as a conventional optical rotary encoder, but utilize a unique encoding pattern that is transmitted through the POF. These sensors are entirely passive, with no electrical power delivered to it, making it intrinsically safe and explosion-proof.
Learn more about the MR431 sensor here.
Strain Detection
Brillouin scattering occurs within a fiber as a light beam propagates through the fiber, interacting with acoustic phonons and generating Stokes light, which is a backscattered light beam. The frequency of the Stokes light is shifted from the center of the incident light’s frequency, in a linear relationship to the force of a strain applied to the fiber. This sensing technique can be incorporated into strain-sensing elements used in building structures and bridges to measure the strain of mechanical loads, or geotextiles, which can monitor sediment movement on slopes.
Field Physiological Monitoring
The i-Protect project has explored the use of fiber optic sensors in personal protective equipment (PPE) worn by fire fighters and rescue workers. The project aimed to create a complete solution that could also monitor external temperature and chemical concentrations, but its physiological sensing component was done through the use of nanotechnology to create conductive paths in fabrics to integrate sensor electronics.
Various sensing techniques were used: Macro bending as a respiratory sensor, photoplethysmography to measure heart rate, and fluorescence lifetime measurement as a temperature sensor.
The high breakdown strength and elasticity of POF make it well-suited for integration in textiles. These sensors and their electronics would then be connected through a wireless link to rescue coordination centers.
pH Level Detection
When the cladding of a POF cable is replaced with a chemical-sensitive material, its refractive index can change in relation to its exposure to chemicals. This is particularly useful for creating immersible pH sensors that modulate transmitted light intensity. The functionality of these sensors depends on the properties of the new cladding, but a cladding incorporating indicator neutral red results in a dynamic range of 2.5 dB between pH 3 and 9.
Hydrogen Sulfide Detection
Researchers at the Photonics and Instrumentation Laboratory at Federal University of Rio de Janeiro developed a hydrogen sulfide (H2S) gas sensor using the refractive index and evanescent field properties of POF. This was achieved by stripping the cladding off of 1.0mm POF and using pulsed laser deposition (PLD) to apply a films of various oxides that react with H2S and change the fiber’s refractive index. This created a relationship between light signal intensity and gas concentration, with sensitivity down to 100ppm. Unlike conventional H2S sensors, no heater is required due to the operational temperature of POF and the associated active components.
References
O. Ziemann et al., POF Handbook. Berlin, Germany: Springer-Verlag Berlin Heidelberg, 2008.
I. López et al., “CHARACTERIZATION OF A POF SENSOR UNDER VIBRATION, FATIGUE LOADS AND TEMPERATURE CONDITIONS” in The 21st International Conference on Plastic Optical Fiber, Atlanta, GA., 2012.
(12 September 2014). What are Fiber Optic Sensors? [Online]. Available: https://www.azosensors.com/article.aspx?ArticleID=333
J. Hopenfeld, “PLASTIC FIBER SENSORS FOR INDUSTRIAL CONTROLS AND ENVIRONMENTAL MONITORING”, POF World, Santa Clara, CA., 2007.
J. Witt et al., “POF SENSORS FOR PERSONAL PROTECTIVE EQUIPMENT (PPE)” in The 21st International Conference on Plastic Optical Fiber, Atlanta, GA., 2012.
L. Bilro; et al., “Optical Sensors Based on Plastic Fibers”. doi: 10.3390/s120912184
N. Hayashi et al., “LARGE STRAIN SENSING USING BRILLOUIN SCATTERING IN PERFLUORINATED GRADED–INDEX POLYMER OPTICAL FIBER” in The 21st International Conference on Plastic Optical Fiber, Atlanta, GA., 2012.
R.C.S.B. Allil, R.N. Lopes, A. Dante, V.V.C. Mota, C.C. Carvalho, M.M. Werneck. “POF-SENSORS APPLICATIONS”, presented at the 27th International Conference on Plastic Optical Fibers, 2018, Seattle, Washington, U.S.A. 2018.
M.M. Keley, A. Dante, F. Dutra, R.C.S.B. Allil, C.C. Carvalho, M.M. Werneck. “FUNCTIONALIZED POF H 2 S SENSOR”, presented at the 27th International Conference on Plastic Optical Fibers, 2018, Seattle, Washington, U.S.A. 2018.